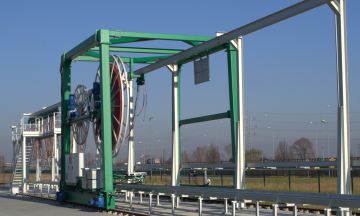
W laboratorium prowadzone są badania nad konstrukcjami przewodów o izolacji i powłoce gumowej, które znajdują zastosowanie w aplikacjach mobilnych wysokich prędkości, wykorzystywanych w urządzeniach przeładunkowych i transportowych. Do tego celu przygotowano specjalistyczną aparaturę suwnicę badawczą, która symuluje rzeczywistą pracę kabli sterowniczych i zasilających w skali 1:1. Uzupełnieniem suwnicy laboratoryjnej jest urządzenie do badania odporności na zginanie w ultraniskich temperaturach, osiągających nawet do −50°C.
2024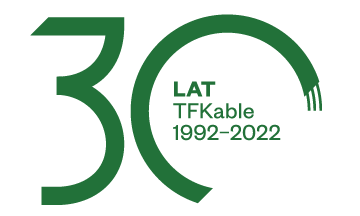
TELE-FONIKA Kable obchodziła przełomowe wydarzenie – trzydziestą rocznicę rozpoczęcia działalności. Przez te 30 lat, od momentu rozpoczęcia działalności w 1992 roku w Myślenicach, firma konsekwentnie budowała nowoczesną TFK.Group, koncentrując się na doświadczeniu i specjalistycznej wiedzy, wykwalifikowanej kadrze oraz innowacjach. Te trzy dekady działalności to również owocna współpraca z partnerami z uczelni, instytutów badawczych i międzynarodowych stowarzyszeń producentów kabli, która wspiera rozwój firmy i całej branży.
2022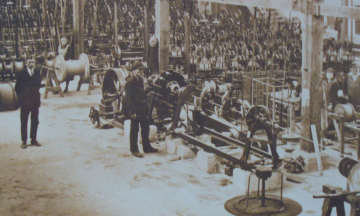
11 listopada 1920 roku, wmurowaniem kamienia węgielnego rozpoczęła się historia Bydgoskiej Fabryki Kabli „Kabel Bydgoszcz”, obecnie – Zakładu Bydgoszcz, Grupa TFKable. Po 100 latach rozwoju technologii, Zakład Bydgoszcz stanowi największe centrum produkcyjne kabli średnich, wysokich i ekstra wysokich napięć w Europie (do 500kV). Zrealizowane na przestrzeni lat inwestycje oraz rozwój technologii produkcji pozwoliły na dołączenie oferty zakładu do licznych globalnych przedsięwzięć. Obchodzący 100-lecie Zakład Bydgoszcz dostarczył kable energetyczne m.in. do takich projektów jak: lotnisko Heathrow, tunel La Manche, stadion Wembley, kopalnie w Peru i Chile i warszawski Stadion Narodowy
2020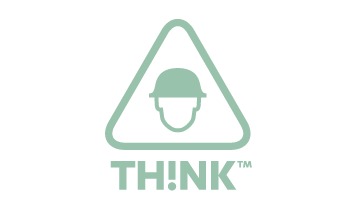
TFK.Group wdrożyło programy TH!NK SAFETY i TH!NK QUALITY, których celem jest zwiększenie świadomości pracowników w zakresie bezpieczeństwa i jakości. TH!NK SAFETY usprawnia komunikację między kadrą zarządzającą a operatorami, eliminując potencjalne zagrożenia, natomiast TH!NK QUALITY koncentruje się na minimalizacji kosztów wynikających z utraty jakości poprzez ciągłe doskonalenie procesów. W 2018 roku pracownicy TFKable zgłosili 561 pomysłów w ramach KAIZEN BHP, a w JDR złożono 186 wniosków usprawniających, co potwierdza skuteczność programów.
2018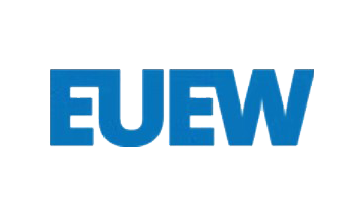
Panel: "Zarządzanie energią i zrównoważony rozwój w przemyśle kablowym" Podczas wystąpienia omówiono kluczowe wyzwania związane z wymogami UE oraz efektywnym zarządzaniem energią. Przedstawiono wdrażane ekologiczne technologie produkcji, strategie oszczędnego gospodarowania zasobami oraz rozwiązania ograniczające emisję zanieczyszczeń. Zaprezentowano również innowacyjne, zautomatyzowane linie produkcyjne oraz nowoczesne produkty, takie jak Flameblocker i Flamex-950, które zapewniają niezawodność systemów kablowych w wymagających warunkach eksploatacyjnych.
2017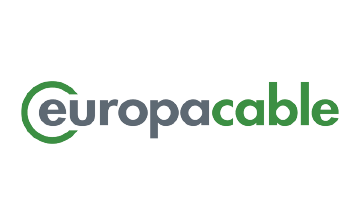
We wrześniu 2015 roku na stanowisko wiceprezydenta Europacable została powołana Pani Monika Cupiał-Zgryzek. Europacable to stowarzyszenie zrzeszające największych europejskich producentów kabli i przewodów.
2015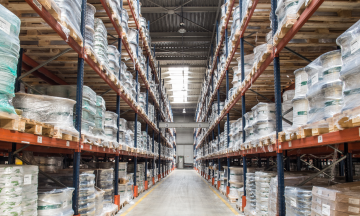
Konsolidacja magazynów – scentralizowano magazyny wyrobów gotowych przy fabrykach, zamknięto magazyny w Czechach, Niemczech i Szwecji, a także utworzono magazyny wyniesione w Wielkiej Brytanii.
2013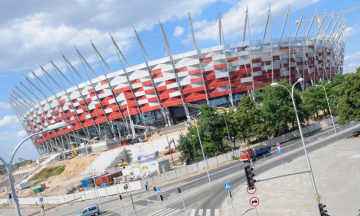
Do zasilania jednej z aren Euro 2012, czyli Stadionu Narodowego w Warszawie, wykorzystano specjalne kable wysokich napięć 110 kV z modułem światłowodowym. W skład linii kablowej wchodzi odcinek ok. 510 m, w którym kable są ułożone pod dnem Wisły w rurze ochronnej, zainstalowanej nowoczesną metodą tzw. wiercenia kierunkowego HDD (horizontal directional drilling – horyzontalny przewiert sterowany).
2011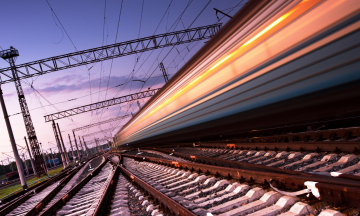
CNTK - Centrum Naukowo-Techniczne Kolejnictwa otrzymała pozwolenie na sieć trakcyjną dużych prędkości, tj. 250 km/h, do której budowy posłużyły wdrożone do produkcji przewody profilowe ze stopu CuAg, wraz z linami nośnymi i wieszakowymi produkowane w zakładzie Kraków-Bieżanów. Specjaliści z TELE-FONIKI Kable, którzy pracowali przy projekcie zostali docenieni nagrodą Prezesa Rady Ministrów.
2008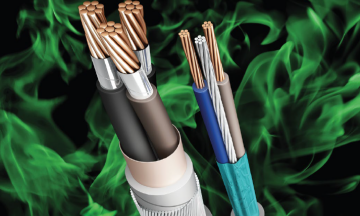
TELE-FONIKA Kable uruchomiła produkcję kabli bezhalogenowych typu FLAME-X Enhanced, Single i POWER. Jako pierwsza firma z Europy Środkowo-Wschodniej uzyskała certyfikat brytyjskiej jednostki certyfikującej LPCB.
2007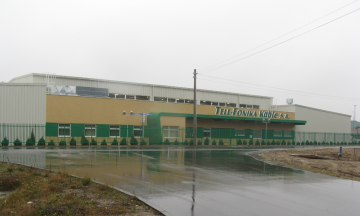
Zgodnie z dyrektywami Unii Europejskiej został oddany do eksploatacji Zakład Recyklingu Odpadów Kablowych w Bukownie. Zakład jest przystosowany do recyklingu ok. 10 tys. ton odpadów kablowych w skali roku. Dzięki zastosowaniu najnowocześniejszych technologii przyjaznych środowisku odzyskuje się w nim frakcje poszczególnych materiałów o czystości ponad 99,5%.
2007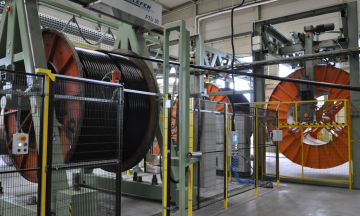
TELE-FONIKA Kable zrealizowała pierwsze zamówienie na produkcję kabli ekstra-wysokich napięć 127/230 kV. Kabel wykonany na zlecenie klienta z Ameryki Południowej został wyprodukowany w zakładzie Bydgoszcz.
2006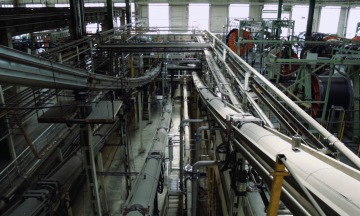
W zakładzie Bydgoszcz uruchomiono 4 nowe linie do produkcji kabli średnich i wysokich napięć w izolacji XLPE. Dzięki temu, Zakład Bydgoszcz stał się największym w Europie producentem kabli średnich i wysokich napięć, produkującym cały asortyment w jednej lokalizacji. Łącznie w zakładzie pracuje 8 linii XLPE.
2002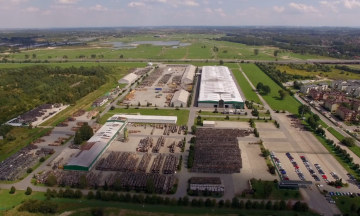
W ramach struktury Zakładów Kablowych TELE-FONIKA S.A. został oddany do eksploatacji nowoczesny, zrobotyzowany zakład Kraków-Bieżanów, specjalizujący się w produkcji: giętkich żył wielodrutowych, żył masowych aluminiowych - wytwarzanych na czterech liniach firmy Holton Conform, przewodów napowietrznych z aluminium stopowego, przewodów trakcyjnych dla szybkich kolei typu „trolley” oraz przewodów w PVC do powszechnych zastosowań.
2001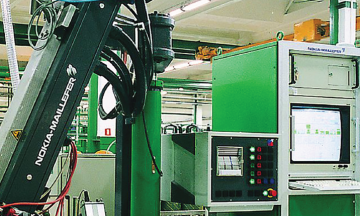
W zakładzie Myślenice rozpoczęto produkcję nowoczesnych kabli światłowodowych. Zakupione zostały urządzenia technologiczne firmy Nokia Maillefer. Tempo instalacji i rozruchu linii produkcyjnej było nieporównywalne z żadną dotychczas znaną instalacją do produkcji światłowodów. Obecnie zakład jest przygotowany do produkcji kabli światłowodowych do 860 włókien w kablu.
1996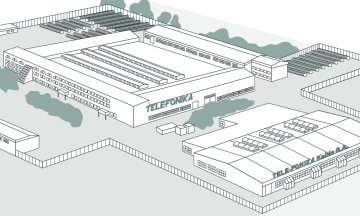
7 kwietnia 1992 roku w Myślenicach został podpisany akt notarialny dotyczący założenia spółki Zakłady Kablowe TELE-FONIKA s.c. W efekcie uruchomiono nowoczesny zakład produkujący kable telekomunikacyjne miedziane, komputerowe i światłowodowe, który zyskał wiodącą pozycję wśród producentów kabli na rynku polskim.
1992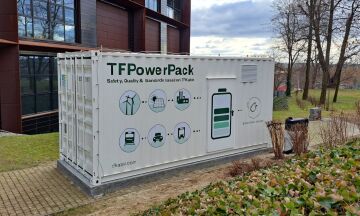
TFPowerPack to magazyn energii, który umożliwia osiągnięcie pełnej niezależności energetycznej. Rozwiązanie Grupy TFKable stanowi kluczowy element redukcji kosztów energii oraz skutecznego zabezpieczenia klientów przed przerwami w dostawie energii. TFPowerPack ułatwia wdrażanie rozwiązań opartych na odnawialnych źródłach energii m.in. poprzez ograniczenie krótkoterminowych wahań mocy z OZE czy wyrównywanie profilu ich pracy przyczyniając się jednocześnie do efektywnej redukcji emisji CO₂.
2023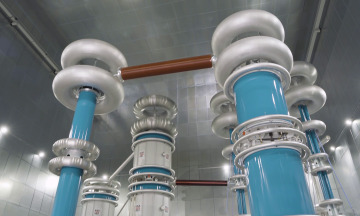
Wyposażone w 5 komór Faradaya do rutynowych i typowych badań kabli oraz systemów kablowych. Laboratorium dysponuje generatorami wysokiego napięcia do 1000 kV oraz generatorami udarowymi do 2400 kV. TFKable posiada dwa własne pola testowe do badań kwalifikacyjnych, wyposażone w systemy testowe 500 kV i 750 kV oraz zestawy transformatorów grzewczych 5000 A. Te nowoczesne laboratoria umożliwiają przeprowadzanie rutynowych testów i pełnych badań kwalifikacyjnych dla kabli do 500 kV. Laboratorium prowadzi również badania prototypów kabli HVDC oraz kabli EHVAC prądu przemiennego z zoptymalizowaną konstrukcją i wytycznymi technologicznymi do ich produkcji.
2021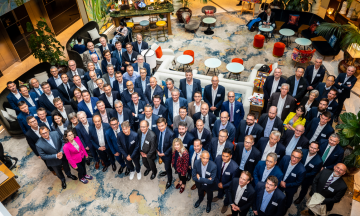
TFKable wspólnie z partnerami stowarzyszonymi w Europacable prowadziło kampanię informacyjną „Ochrona przeciwpożarowa to nasza odpowiedzialność. Twoja też”, związaną z Construction Products Regulation (CPR). Celem inicjatywy było poinformowanie o nowych przepisach dotyczących kabli przeznaczonych do trwałego instalowania w obiektach budowlanych, a obecnie podlegających wymaganiom zawartym w CPR. Kampania dawała możliwość szybkiego dostępu do przydatnych informacji, które w założeniu miały ułatwić spełnienie nowych obowiązków przez instalatorów, producentów i hurtowników. Jej głównym założeniem było promowanie rozwiązań technologicznych w zakresie bezpieczeństwa pożarowego w Europie.
2019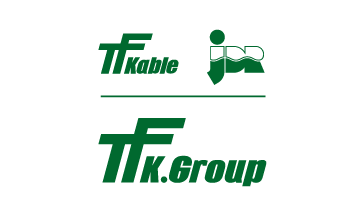
W efekcie nabycia JDR Cable Systems (Holdings) Ltd., Grupa TFKable zwiększyła posiadane aktywa o dwa zakłady produkcyjne zlokalizowane w Wielkiej Brytanii, specjalizujące się w dostarczaniu podmorskich kabli zasilających oraz kabli magistralowych (tzw. umbilicals), które zawierają zarówno kable energetyczne, jak i do przesyłania danych, służące monitoringowi i zdalnemu sterowaniu, mające zastosowanie w konstrukcjach offshore. Ponadto nasza oferta handlowa została poszerzona o zaawansowaną technologicznie produkcję systemów podmorskich oraz o usługi serwisowe i instalacyjne, zlokalizowane w oddziałach w USA, Brazylii i Singapurze, które zapewniają stałe wsparcie naszym partnerom handlowym.
2017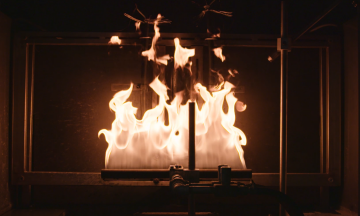
Rozpoczęto działania, mające na celu wprowadzenie zmian, w odniesieniu do bezpieczeństwa pożarowego dla kabli i przewodów zharmonizowanych w normie europejskiej EN 50575:2014, której data wdrożenia została przyjęta na dzień 01 lipca 2017 r.
2016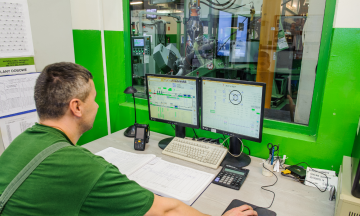
Wdrożono system informatyczny SAP APO do zaawansowanego planowania produkcji i harmonogramowania w przemyśle kablowym.
2015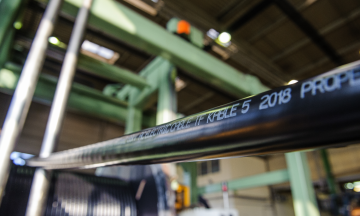
Od stycznia 2012 do lutego 2013 roku w Grupie TELE-FONIKA Kable prowadzony był projekt, mający na celu pełną specjalizację produkcji. Tym samym, przeprowadzono przemieszczenie maszyn pomiędzy zakładami, a także wewnątrz nich. W efekcie, stworzono gniazda produkcyjne ograniczające transport wewnętrzny poprzez skrócenie cykli produkcyjnych i zmniejszenie ilości zapasów.
2012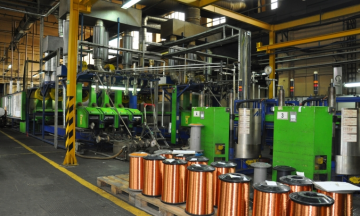
TELE-FONIKA Kable, jako pierwszy producent w Polsce i jeden z nielicznych w Europie, uruchomiła w zakładzie Szczecin produkcję aluminiowych przewodów nawojowych Al 200. Zamówione przewody zostały wykorzystane do produkcji transformatorów. Początkowo możliwe było produkowanie przewodów o średnicy 2–3,55 mm, obecnie uzyskiwane są średnice 0,3–4 mm.
2009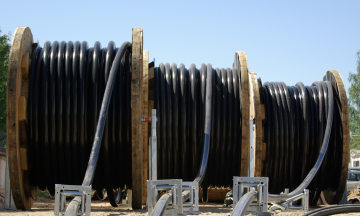
TELE-FONIKA Kable zrealizowała pierwsze zamówienie na produkcję hybrydowych kabli wysokich napięć 64/110 kV. W kablu zainstalowany został moduł światłowodowy do pomiaru temperatury kabla. Zamówione kable zostały dostarczone do Chile.
2008
W wyniku akwizycji w skład Grupy TELE-FONIKA weszła Fabrika Kablova Zajecar d.o.o. zlokalizowana w Serbii. Zakład specjalizuje się w produkcji kabli niskich i średnich napięć, kabli telekomunikacyjnych oraz przewodów.
2007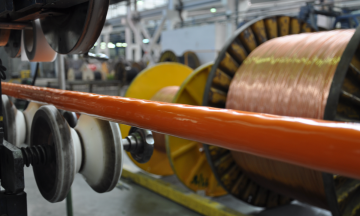
W zakładzie Kraków uruchomiono produkcję kabli górniczych typu SHD i GGC w powłokach gumowych i poliuretanowych. Znaczące inwestycje pozwoliły na uruchomienie 15 linii CV. Dzięki temu, zakład został największym ośrodkiem produkcji kabli w gumie w Europie.
2006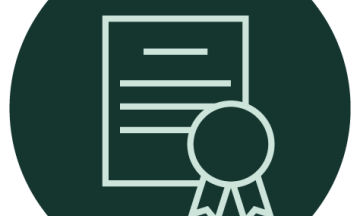
Certyfikaty <HAR> , uprawniają do znakowania wyrobów zharmonizowanym znakiem europejskim potwierdzającym, że oznaczone przewody o izolacji polwinitowej oraz na przewody o izolacji gumowej, spełniają wymagania właściwych norm europejskich (EN) i dokumentów zharmonizowanych (HD).
2003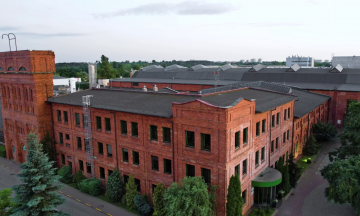
Spółka TELE-FONIKA KFK S.A. zakupiła pakiet większościowy spółki ELEKTRIM Kable S.A. W 2003 roku, w związku z objęciem całego pakietu akcji ELEKTRIM Kable S.A., powstał nowy podmiot TELE-FONIKA Kable S.A. W wyniku przeprowadzonych akwizycji w Grupie TELE-FONIKA znalazły się: Bydgoska Fabryka Kabli (BFK) – założona w 1920 roku, specjalizująca się w produkcji kabli niskich, średnich, wysokich i ekstrawysokich napięć oraz Fabryka Kabli Załom (FKZ) - założona w 1954 roku, specjalizująca się w produkcji przewodów nawojowych emaliowanych.
2001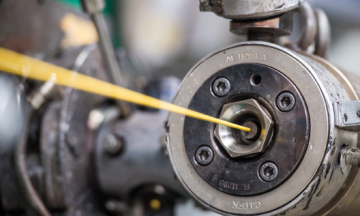
22 stycznia 1999 roku TELE-FONIKA s.c. objęła większościowy pakiet akcji Krakowskiej Fabryki Kabli SA (KFK), zaś do końca 2001 roku sfinalizowano zakup 100% akcji spółki. Fabryka KFK powstała w 1928 roku i była największym w Polsce wytwórcą kabli i przewodów elektroenergetycznych. W 1992 roku otrzymała certyfikat ISO przyznany przez BASEC Anglia. Specjalnością produkcyjną zakładu są kable i przewody w gumie.
1999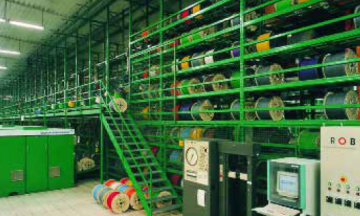
W zakładzie Myślenice rozpoczęto produkcję nowoczesnych kabli telekomunikacyjnych miedzianych. Czteroparowe kable komputerowe UTP i FTP kat. 5 pozwalają na przenoszenie danych w paśmie do 100 MHz i przepływ do 1 Gbit/s. W związku z dużym zapotrzebowaniem rynku, w ciągu roku podwojono zdolności produkcyjne w tym asortymencie.
1995W laboratorium prowadzone są badania nad konstrukcjami przewodów o izolacji i powłoce gumowej, które znajdują zastosowanie w aplikacjach mobilnych wysokich prędkości, wykorzystywanych w urządzeniach przeładunkowych i transportowych. Do tego celu przygotowano specjalistyczną aparaturę suwnicę badawczą, która symuluje rzeczywistą pracę kabli sterowniczych i zasilających w skali 1:1. Uzupełnieniem suwnicy laboratoryjnej jest urządzenie do badania odporności na zginanie w ultraniskich temperaturach, osiągających nawet do −50°C.
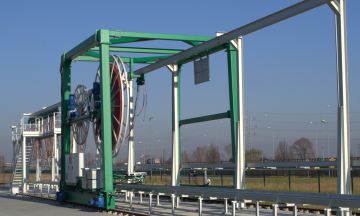
TFPowerPack to magazyn energii, który umożliwia osiągnięcie pełnej niezależności energetycznej. Rozwiązanie Grupy TFKable stanowi kluczowy element redukcji kosztów energii oraz skutecznego zabezpieczenia klientów przed przerwami w dostawie energii. TFPowerPack ułatwia wdrażanie rozwiązań opartych na odnawialnych źródłach energii m.in. poprzez ograniczenie krótkoterminowych wahań mocy z OZE czy wyrównywanie profilu ich pracy przyczyniając się jednocześnie do efektywnej redukcji emisji CO₂.
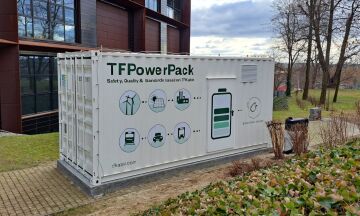
TELE-FONIKA Kable obchodziła przełomowe wydarzenie – trzydziestą rocznicę rozpoczęcia działalności. Przez te 30 lat, od momentu rozpoczęcia działalności w 1992 roku w Myślenicach, firma konsekwentnie budowała nowoczesną TFK.Group, koncentrując się na doświadczeniu i specjalistycznej wiedzy, wykwalifikowanej kadrze oraz innowacjach. Te trzy dekady działalności to również owocna współpraca z partnerami z uczelni, instytutów badawczych i międzynarodowych stowarzyszeń producentów kabli, która wspiera rozwój firmy i całej branży.
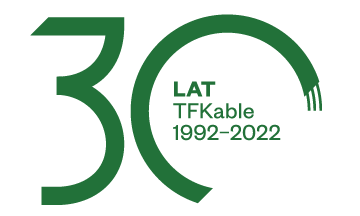
Wyposażone w 5 komór Faradaya do rutynowych i typowych badań kabli oraz systemów kablowych. Laboratorium dysponuje generatorami wysokiego napięcia do 1000 kV oraz generatorami udarowymi do 2400 kV. TFKable posiada dwa własne pola testowe do badań kwalifikacyjnych, wyposażone w systemy testowe 500 kV i 750 kV oraz zestawy transformatorów grzewczych 5000 A. Te nowoczesne laboratoria umożliwiają przeprowadzanie rutynowych testów i pełnych badań kwalifikacyjnych dla kabli do 500 kV. Laboratorium prowadzi również badania prototypów kabli HVDC oraz kabli EHVAC prądu przemiennego z zoptymalizowaną konstrukcją i wytycznymi technologicznymi do ich produkcji.
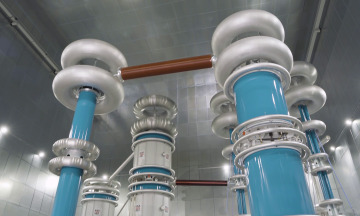
11 listopada 1920 roku, wmurowaniem kamienia węgielnego rozpoczęła się historia Bydgoskiej Fabryki Kabli „Kabel Bydgoszcz”, obecnie – Zakładu Bydgoszcz, Grupa TFKable. Po 100 latach rozwoju technologii, Zakład Bydgoszcz stanowi największe centrum produkcyjne kabli średnich, wysokich i ekstra wysokich napięć w Europie (do 500kV). Zrealizowane na przestrzeni lat inwestycje oraz rozwój technologii produkcji pozwoliły na dołączenie oferty zakładu do licznych globalnych przedsięwzięć. Obchodzący 100-lecie Zakład Bydgoszcz dostarczył kable energetyczne m.in. do takich projektów jak: lotnisko Heathrow, tunel La Manche, stadion Wembley, kopalnie w Peru i Chile i warszawski Stadion Narodowy
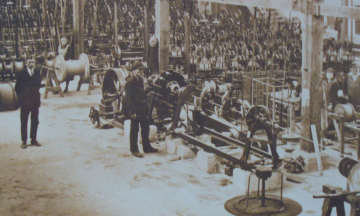
TFKable wspólnie z partnerami stowarzyszonymi w Europacable prowadziło kampanię informacyjną „Ochrona przeciwpożarowa to nasza odpowiedzialność. Twoja też”, związaną z Construction Products Regulation (CPR). Celem inicjatywy było poinformowanie o nowych przepisach dotyczących kabli przeznaczonych do trwałego instalowania w obiektach budowlanych, a obecnie podlegających wymaganiom zawartym w CPR. Kampania dawała możliwość szybkiego dostępu do przydatnych informacji, które w założeniu miały ułatwić spełnienie nowych obowiązków przez instalatorów, producentów i hurtowników. Jej głównym założeniem było promowanie rozwiązań technologicznych w zakresie bezpieczeństwa pożarowego w Europie.
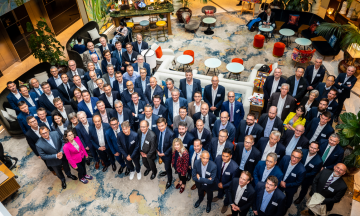
TFK.Group wdrożyło programy TH!NK SAFETY i TH!NK QUALITY, których celem jest zwiększenie świadomości pracowników w zakresie bezpieczeństwa i jakości. TH!NK SAFETY usprawnia komunikację między kadrą zarządzającą a operatorami, eliminując potencjalne zagrożenia, natomiast TH!NK QUALITY koncentruje się na minimalizacji kosztów wynikających z utraty jakości poprzez ciągłe doskonalenie procesów. W 2018 roku pracownicy TFKable zgłosili 561 pomysłów w ramach KAIZEN BHP, a w JDR złożono 186 wniosków usprawniających, co potwierdza skuteczność programów.
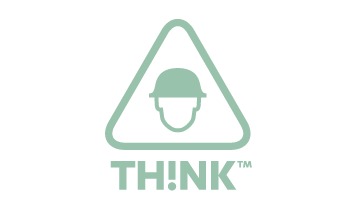
W efekcie nabycia JDR Cable Systems (Holdings) Ltd., Grupa TFKable zwiększyła posiadane aktywa o dwa zakłady produkcyjne zlokalizowane w Wielkiej Brytanii, specjalizujące się w dostarczaniu podmorskich kabli zasilających oraz kabli magistralowych (tzw. umbilicals), które zawierają zarówno kable energetyczne, jak i do przesyłania danych, służące monitoringowi i zdalnemu sterowaniu, mające zastosowanie w konstrukcjach offshore. Ponadto nasza oferta handlowa została poszerzona o zaawansowaną technologicznie produkcję systemów podmorskich oraz o usługi serwisowe i instalacyjne, zlokalizowane w oddziałach w USA, Brazylii i Singapurze, które zapewniają stałe wsparcie naszym partnerom handlowym.
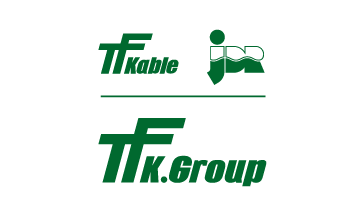
Panel: "Zarządzanie energią i zrównoważony rozwój w przemyśle kablowym" Podczas wystąpienia omówiono kluczowe wyzwania związane z wymogami UE oraz efektywnym zarządzaniem energią. Przedstawiono wdrażane ekologiczne technologie produkcji, strategie oszczędnego gospodarowania zasobami oraz rozwiązania ograniczające emisję zanieczyszczeń. Zaprezentowano również innowacyjne, zautomatyzowane linie produkcyjne oraz nowoczesne produkty, takie jak Flameblocker i Flamex-950, które zapewniają niezawodność systemów kablowych w wymagających warunkach eksploatacyjnych.
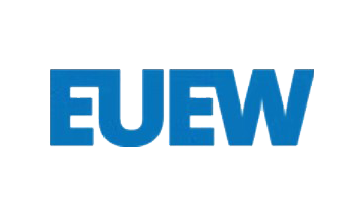
Rozpoczęto działania, mające na celu wprowadzenie zmian, w odniesieniu do bezpieczeństwa pożarowego dla kabli i przewodów zharmonizowanych w normie europejskiej EN 50575:2014, której data wdrożenia została przyjęta na dzień 01 lipca 2017 r.
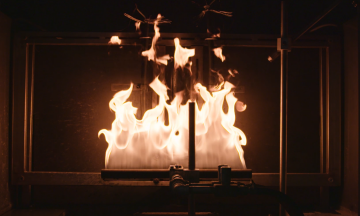
We wrześniu 2015 roku na stanowisko wiceprezydenta Europacable została powołana Pani Monika Cupiał-Zgryzek. Europacable to stowarzyszenie zrzeszające największych europejskich producentów kabli i przewodów.
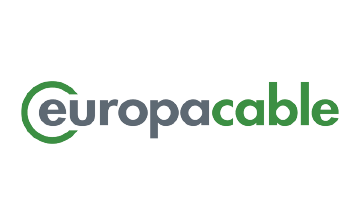
Wdrożono system informatyczny SAP APO do zaawansowanego planowania produkcji i harmonogramowania w przemyśle kablowym.
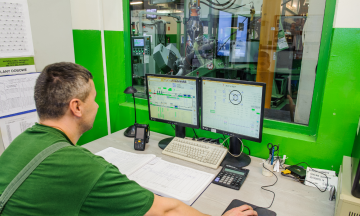
Konsolidacja magazynów – scentralizowano magazyny wyrobów gotowych przy fabrykach, zamknięto magazyny w Czechach, Niemczech i Szwecji, a także utworzono magazyny wyniesione w Wielkiej Brytanii.
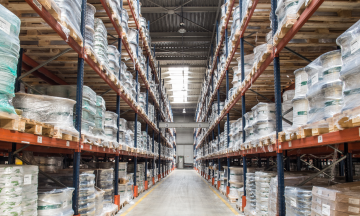
Od stycznia 2012 do lutego 2013 roku w Grupie TELE-FONIKA Kable prowadzony był projekt, mający na celu pełną specjalizację produkcji. Tym samym, przeprowadzono przemieszczenie maszyn pomiędzy zakładami, a także wewnątrz nich. W efekcie, stworzono gniazda produkcyjne ograniczające transport wewnętrzny poprzez skrócenie cykli produkcyjnych i zmniejszenie ilości zapasów.
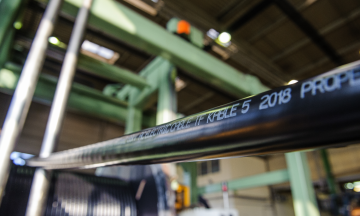
Do zasilania jednej z aren Euro 2012, czyli Stadionu Narodowego w Warszawie, wykorzystano specjalne kable wysokich napięć 110 kV z modułem światłowodowym. W skład linii kablowej wchodzi odcinek ok. 510 m, w którym kable są ułożone pod dnem Wisły w rurze ochronnej, zainstalowanej nowoczesną metodą tzw. wiercenia kierunkowego HDD (horizontal directional drilling – horyzontalny przewiert sterowany).
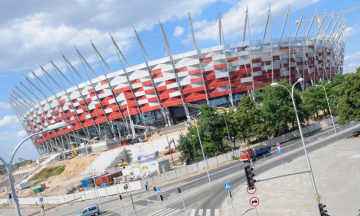
TELE-FONIKA Kable, jako pierwszy producent w Polsce i jeden z nielicznych w Europie, uruchomiła w zakładzie Szczecin produkcję aluminiowych przewodów nawojowych Al 200. Zamówione przewody zostały wykorzystane do produkcji transformatorów. Początkowo możliwe było produkowanie przewodów o średnicy 2–3,55 mm, obecnie uzyskiwane są średnice 0,3–4 mm.
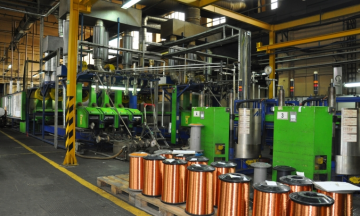
CNTK - Centrum Naukowo-Techniczne Kolejnictwa otrzymała pozwolenie na sieć trakcyjną dużych prędkości, tj. 250 km/h, do której budowy posłużyły wdrożone do produkcji przewody profilowe ze stopu CuAg, wraz z linami nośnymi i wieszakowymi produkowane w zakładzie Kraków-Bieżanów. Specjaliści z TELE-FONIKI Kable, którzy pracowali przy projekcie zostali docenieni nagrodą Prezesa Rady Ministrów.
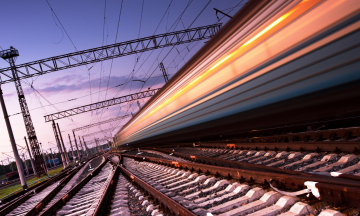
TELE-FONIKA Kable zrealizowała pierwsze zamówienie na produkcję hybrydowych kabli wysokich napięć 64/110 kV. W kablu zainstalowany został moduł światłowodowy do pomiaru temperatury kabla. Zamówione kable zostały dostarczone do Chile.
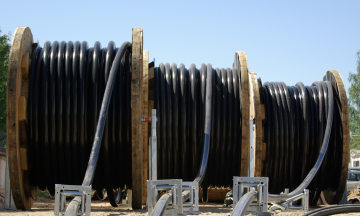
TELE-FONIKA Kable uruchomiła produkcję kabli bezhalogenowych typu FLAME-X Enhanced, Single i POWER. Jako pierwsza firma z Europy Środkowo-Wschodniej uzyskała certyfikat brytyjskiej jednostki certyfikującej LPCB.
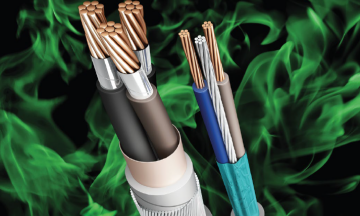
W wyniku akwizycji w skład Grupy TELE-FONIKA weszła Fabrika Kablova Zajecar d.o.o. zlokalizowana w Serbii. Zakład specjalizuje się w produkcji kabli niskich i średnich napięć, kabli telekomunikacyjnych oraz przewodów.

Zgodnie z dyrektywami Unii Europejskiej został oddany do eksploatacji Zakład Recyklingu Odpadów Kablowych w Bukownie. Zakład jest przystosowany do recyklingu ok. 10 tys. ton odpadów kablowych w skali roku. Dzięki zastosowaniu najnowocześniejszych technologii przyjaznych środowisku odzyskuje się w nim frakcje poszczególnych materiałów o czystości ponad 99,5%.
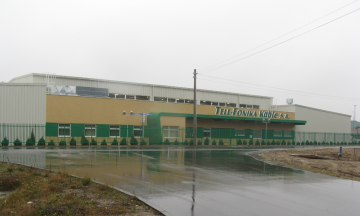
W zakładzie Kraków uruchomiono produkcję kabli górniczych typu SHD i GGC w powłokach gumowych i poliuretanowych. Znaczące inwestycje pozwoliły na uruchomienie 15 linii CV. Dzięki temu, zakład został największym ośrodkiem produkcji kabli w gumie w Europie.
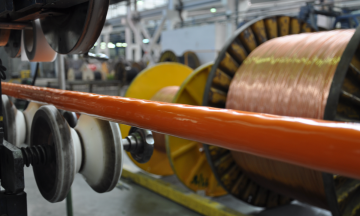
TELE-FONIKA Kable zrealizowała pierwsze zamówienie na produkcję kabli ekstra-wysokich napięć 127/230 kV. Kabel wykonany na zlecenie klienta z Ameryki Południowej został wyprodukowany w zakładzie Bydgoszcz.
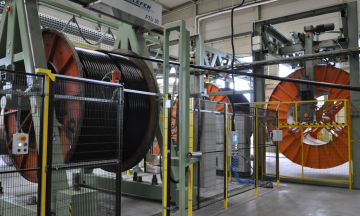
Certyfikaty <HAR> , uprawniają do znakowania wyrobów zharmonizowanym znakiem europejskim potwierdzającym, że oznaczone przewody o izolacji polwinitowej oraz na przewody o izolacji gumowej, spełniają wymagania właściwych norm europejskich (EN) i dokumentów zharmonizowanych (HD).
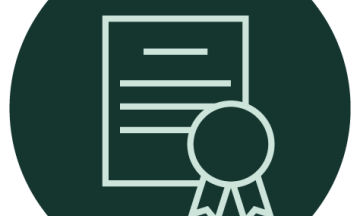
W zakładzie Bydgoszcz uruchomiono 4 nowe linie do produkcji kabli średnich i wysokich napięć w izolacji XLPE. Dzięki temu, Zakład Bydgoszcz stał się największym w Europie producentem kabli średnich i wysokich napięć, produkującym cały asortyment w jednej lokalizacji. Łącznie w zakładzie pracuje 8 linii XLPE.
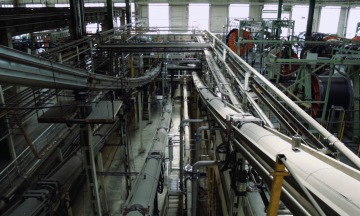
Spółka TELE-FONIKA KFK S.A. zakupiła pakiet większościowy spółki ELEKTRIM Kable S.A. W 2003 roku, w związku z objęciem całego pakietu akcji ELEKTRIM Kable S.A., powstał nowy podmiot TELE-FONIKA Kable S.A. W wyniku przeprowadzonych akwizycji w Grupie TELE-FONIKA znalazły się: Bydgoska Fabryka Kabli (BFK) – założona w 1920 roku, specjalizująca się w produkcji kabli niskich, średnich, wysokich i ekstrawysokich napięć oraz Fabryka Kabli Załom (FKZ) - założona w 1954 roku, specjalizująca się w produkcji przewodów nawojowych emaliowanych.
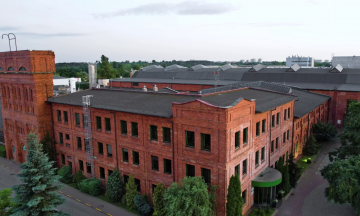
W ramach struktury Zakładów Kablowych TELE-FONIKA S.A. został oddany do eksploatacji nowoczesny, zrobotyzowany zakład Kraków-Bieżanów, specjalizujący się w produkcji: giętkich żył wielodrutowych, żył masowych aluminiowych - wytwarzanych na czterech liniach firmy Holton Conform, przewodów napowietrznych z aluminium stopowego, przewodów trakcyjnych dla szybkich kolei typu „trolley” oraz przewodów w PVC do powszechnych zastosowań.
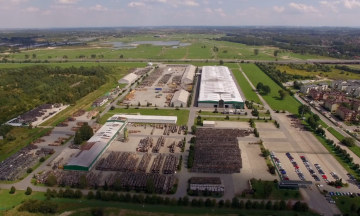
22 stycznia 1999 roku TELE-FONIKA s.c. objęła większościowy pakiet akcji Krakowskiej Fabryki Kabli SA (KFK), zaś do końca 2001 roku sfinalizowano zakup 100% akcji spółki. Fabryka KFK powstała w 1928 roku i była największym w Polsce wytwórcą kabli i przewodów elektroenergetycznych. W 1992 roku otrzymała certyfikat ISO przyznany przez BASEC Anglia. Specjalnością produkcyjną zakładu są kable i przewody w gumie.
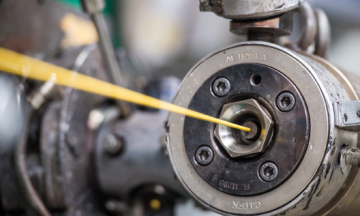
W zakładzie Myślenice rozpoczęto produkcję nowoczesnych kabli światłowodowych. Zakupione zostały urządzenia technologiczne firmy Nokia Maillefer. Tempo instalacji i rozruchu linii produkcyjnej było nieporównywalne z żadną dotychczas znaną instalacją do produkcji światłowodów. Obecnie zakład jest przygotowany do produkcji kabli światłowodowych do 860 włókien w kablu.
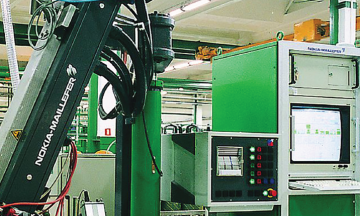
W zakładzie Myślenice rozpoczęto produkcję nowoczesnych kabli telekomunikacyjnych miedzianych. Czteroparowe kable komputerowe UTP i FTP kat. 5 pozwalają na przenoszenie danych w paśmie do 100 MHz i przepływ do 1 Gbit/s. W związku z dużym zapotrzebowaniem rynku, w ciągu roku podwojono zdolności produkcyjne w tym asortymencie.
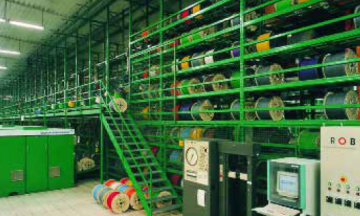
7 kwietnia 1992 roku w Myślenicach został podpisany akt notarialny dotyczący założenia spółki Zakłady Kablowe TELE-FONIKA s.c. W efekcie uruchomiono nowoczesny zakład produkujący kable telekomunikacyjne miedziane, komputerowe i światłowodowe, który zyskał wiodącą pozycję wśród producentów kabli na rynku polskim.
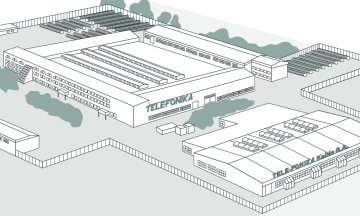