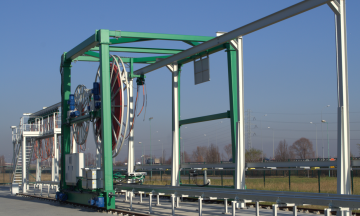
The laboratory conducts research on the construction of rubber-insulated and sheathed conductors used in high-speed mobile applications, such as handling and transportation equipment. For this purpose, specialized equipment, including a research gantry crane, has been prepared to simulate the real operation of control and power cables on a 1:1 scale. The laboratory gantry crane is complemented by a device for testing bending resistance at ultra-low temperatures, reaching as low as −50°C.
2024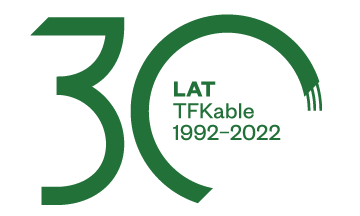
TELE-FONIKA Kable celebrated a significant milestone – the thirtieth anniversary of its founding. Over these 30 years, since beginning operations in 1992 in Myślenice, the company has consistently built a modern TFK.Group, focusing on experience, specialized knowledge, a skilled workforce, and innovation. These three decades of operations also include fruitful collaboration with partners from universities, research institutes, and international cable manufacturers' associations, which supports the development of the company and the entire industry.
2022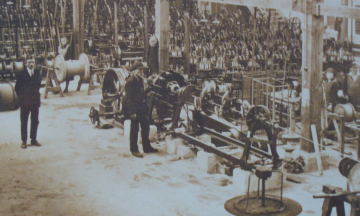
On November 11, 1920, the foundation stone laying ceremony started the history of the Bydgoszcz Plant "Kabel Bydgoszcz", currently - Zakład Bydgoszcz (Bydgoszcz Plant), TFKable Group. Nowadays, after 100 years of technology development, Zakład Bydgoszcz is the largest production center for medium, high and extra-high voltage cables in Europe (up to 500kV). Thanks to investments made over the years, Zakład Bydgoszcz delivered power cables to numerous global projects. In its rich history, the plant provided power cables for such projects as London Heathrow Airport, Channel Tunnel, Wembley Stadium, mines in Peru and Chile and the National Stadium in Warsaw.
2020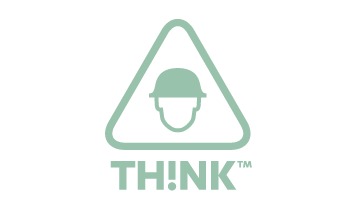
TFK.Group has implemented the TH!NK SAFETY and TH!NK QUALITY programs to raise employee awareness of safety and quality. TH!NK SAFETY enhances communication between management and operators, eliminating potential hazards, while TH!NK QUALITY focuses on minimizing costs related to quality loss through continuous process improvement. In 2018, TFKable employees submitted 561 ideas under the KAIZEN HSE initiative, while JDR received 186 improvement proposals, confirming the effectiveness of these programs.
2018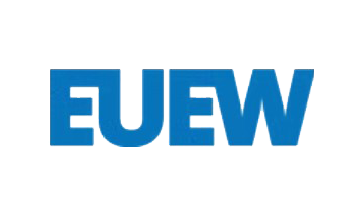
Panel: "Energy Management and Sustainability in the Cable Industry" The presentation addressed key challenges related to EU regulations and effective energy management. It highlighted the implementation of eco-friendly production technologies, resource-efficient strategies, and solutions to reduce pollutant emissions. Innovative automated production lines and advanced products, such as Flameblocker and Flamex-950, were also introduced, ensuring cable system reliability in demanding operating conditions.
2017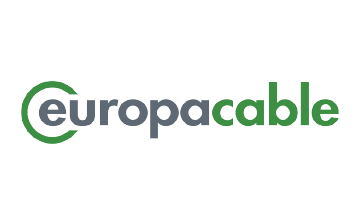
TELE-FONIKA Kable S.A. became an active member of Europacable, the association of the largest European producers of conduits and cables. Since September 2015, Mrs. Monika Cupiał-Zgryzek has been Vice-President of Europacable.
2015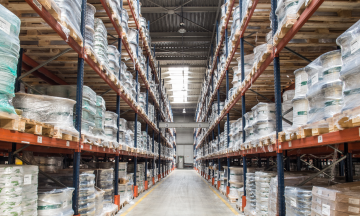
Warehouse consolidation – warehouses were centralized finished products at factories, warehouses in the Czech Republic were closed, Germany and Sweden as well elevated warehouses were created in Great Britain
2013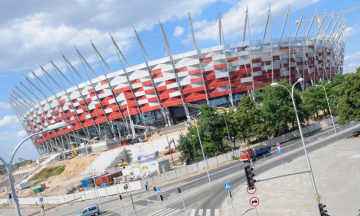
To power the National Stadium in Warsaw as one of the arenas of Euro 2012, special high voltage 110 kV cables with fibre modules were used. The cable line included a section of approximately 510 m, in which the cables were arranged under the Vistula River in a protective pipe, installed using a modern HDD (horizontal directional drilling) method.
2011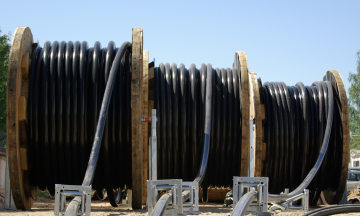
TF Kable fulfilled the first order for the production of hybrid high voltage cables of 64/110 kV. The cables included a fibre optic module to measure its temperature. Ordered cables were delivered to Chile.
2008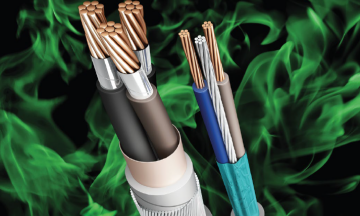
TELE-FONIKA Kable has launched the production of halogen-free FLAME-X Enhanced, Single, and POWER cables. It is the first company from Central and Eastern Europe to obtain certification from the UK certification body LPCB.
2007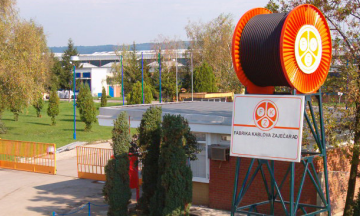
As a result of the acquisition, TF Kable now includes Fabrika Kablova Zajecar d.o.o. located in Serbia. The plant specialises in the production of low and medium voltage cables, telecommunication cables and wires.
2007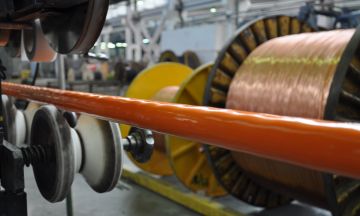
The production of mining cables of SHD and GGC types, in rubber and polyurethane coatings began at the plant in Kraków. Significant investment allowed for the installation of 15 CV lines, making the plant the largest centre for rubber cable production in Europe.
2006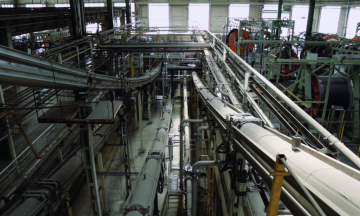
Four new production lines were developed in Bydgoszcz to produce medium and high voltage cables in XLPE insulation. The plant in Bydgoszcz became the largest producer of medium and high voltage cables in one location in Europe. In total, plant operates eight XLPE lines.
2002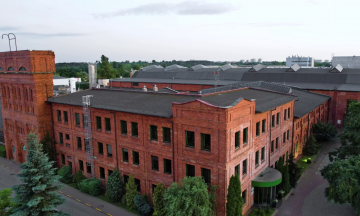
TELE-FONIKA KFK S.A. purchased the majority stake of ELEKTRIM Kable S.A. In 2003, after purchasing all shares of ELEKTRIM Kable S.A., a new entity, TELE-FONIKA Kable S.A., was established. As a result of the acquisition, TELE-FONIKA Group included: Bydgoska Fabryka Kabli (BFK), founded in 1920, specialising in the production of low, medium, high and extra high voltage cables and Fabryka Kabli Załom (FKZ), established in 1954, specialising in the production of enamelled winding conduits.
2001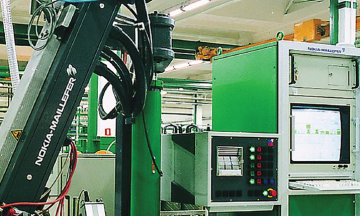
The production of modern fibre optic cables began in the plant in Myślenice after the purchase of technical equipment from Nokia Maillefer. The pace of installation and commissioning of the production line eclipsed any previously known system for producing optical fibres. At this point, the plant was ready to produce fibre optic cables with up to 860 fibres per cable
1996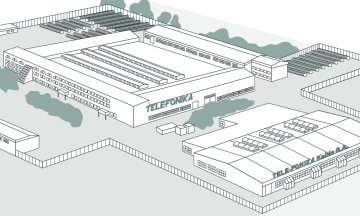
A notarial deed was signed to establish Zakłady Kablowe TELE-FONIKA s.c. on 7 April 1992 in Myślenice. Soon after, a modern plant began producing copper telecommunication, computer and fibre optic cables, within a short time becoming the leading cable producer in the Polish market.
1992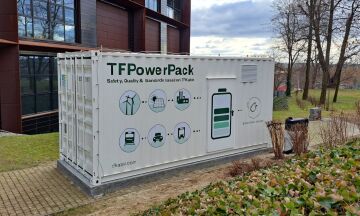
TFPowerPack is an energy storage solution that enables full energy independence. TFKable Group's solution is a key element in reducing energy costs and effectively protecting customers from power outages. TFPowerPack facilitates the implementation of solutions based on renewable energy sources, including limiting short-term power fluctuations from RES and balancing their operational profile, thus contributing to efficient CO₂ emissions reduction.
2023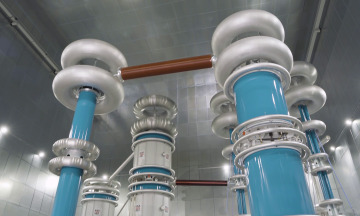
The laboratory is equipped with 5 Faraday chambers for routine and type tests of cables and cable systems. It features high voltage generators up to 1000 kV and surge generators up to 2400 kV. TFKable has two dedicated test fields for qualification tests, equipped with 500 kV and 750 kV test systems and 5000 A heating transformer sets. These state-of-the-art laboratories enable the performance of routine tests and full qualification tests for cables up to 500 kV. The laboratory also conducts research on prototypes of HVDC cables and EHVAC alternating current cables with optimized construction and technological guidelines for their production.
2021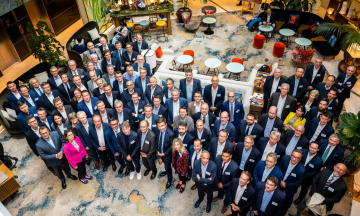
TFKable together with the partners associated in the Europacable conducted the campaign "Fire safety is our responsibility. Yours too”, related to the Construction Products Regulation (CPR). The initiative aimed to inform on a large scale about new regulations concerning cables intended for permanent installation in buildings and currently subject to the requirements of the CPR regulation. The campaign provided easy access to useful information that was intended to help installers, manufacturers, and wholesalers meet the new requirements.
2019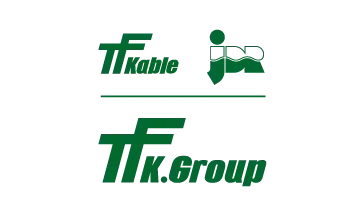
As a result of JDR’s acquisition, TF Kable has expanded its assets with two UK production facilitates, which specialize in producing subsea umbilicals and power cables, including not only energy cables but also cables used for data transmission, and monitoring and remote control of offshore facilities. Additionally, sales portfolio has been extended by technologically advanced subsea systems, maintenance and installation services, located in JDR’s centers in the US, Brazil and Singapore, ensuring constant support for our business partners.
2017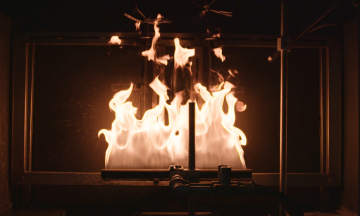
Actions, concerning the implementation of changes in relations to fire safety for cables and wires harmonized in European Standard EN 50575:2014, have been started. The implementation date for this standard was determined as of July 1, 2017.
2016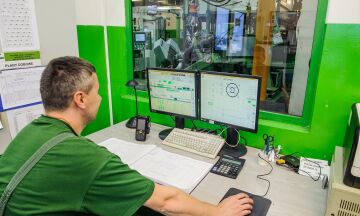
The SAP APO system was implemented for advanced production planning and scheduling for the cable industry.
2015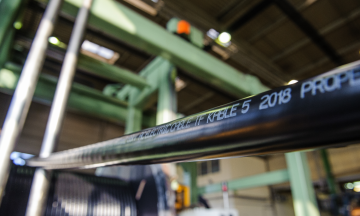
From January 2012 to February 2013, the group carried out the production specialisation project. The specialisation optimised placement of machines between and inside the plants. The aim was to create production slots limiting internal transport by shortening the production cycles and reducing the amount of stock.
2012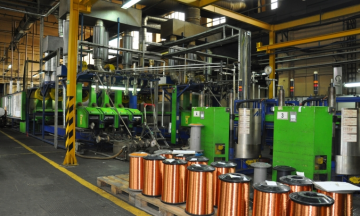
TF Kable, as the first producer in Poland and one of the few in Europe, started the production of aluminium winding conduits Al 200 in the plant in Szczecin. The conduits were used for the production of transformers. Initially, it was possible to produce conduits of 2-3.55 mm diameter; now, the diameters are 0.3-4 mm.
2009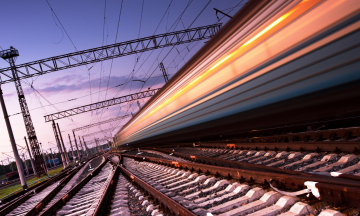
CNTK (Scientific and Technical Railway Centre) was granted the project for a high-speed, 250 km/h railway network, the construction of which involved the production of profile cables made of CuAg alloy, with the supporting lines and hanging lines produced in the plant in Kraków-Bieżanów. The team, including specialists from TF Kable, was awarded the project by the Prime Minister.
2008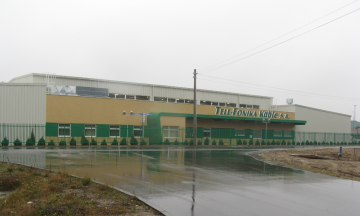
In accordance with the directives of the European Union, the Cable Waste Recycling Plant was launched in Bukowno. The plant is designed to recycle approximately 10,000 tonnes of cable waste per year. By using the latest environmentally friendly technologies, fractions of each material with a purity of over 99.5% are recovered.
2007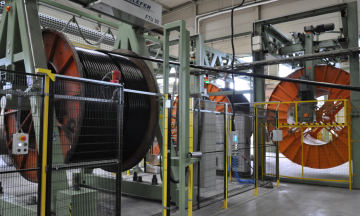
TF Kable fulfils the first order for extra high voltage cables of 127/230 kV. The cable was produced in the Bydgoszcz plant at the order of a customer from South America.
2006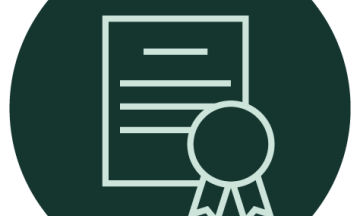
TF Kable was the first company in Poland to obtain <HAR> certificates for conduits in PVC insulation and in rubber insulation. They allow the company to mark its products with the harmonised European mark certifying that the marked conduits meet the requirements of the relevant European Standards (EN) or the harmonised documents (HD).
2003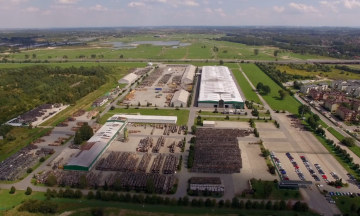
Within the structure of Zakłady Kablowe TELE-FONIKA S.A., a modern robotic plant was launched in Kraków-Bieżanów , specialising in the production of flexible multi-wire cores, aluminium mass cores produced on four lines by Holton Conform, overhead conduits made of aluminium alloy, traction conduits for high-speed “trolley” type rail and conduits in PVC for common applications.
2001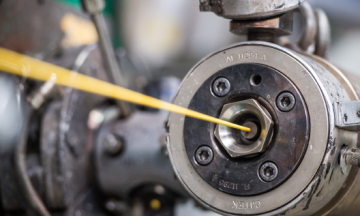
On 22 January 1999, TELE-FONIKA s.c. acquired the majority of shares in Krakowska Fabryka Kabli SA (KFK), with 100% of the company purchased by the end of 2001. The factory was established in 1928, and was the largest Polish producer of power cables and conduits. In 1992, it obtained the ISO certificate granted by BASEC, England. Rubber cables and conduits are the plant’s top products.
1999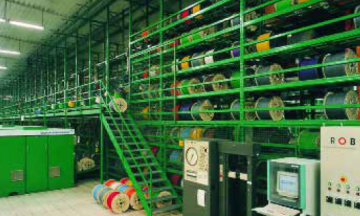
The production of modern telecommunication copper cables began in the plant in Myślenice. These four-pair computer UTP and FTP cables of cat. 5 enabled the transfer of data in a band up to 100 MHz and flow of 1 Gbit/s. The market demand was so high that the production capacity in this range doubled within a year.
1995The laboratory conducts research on the construction of rubber-insulated and sheathed conductors used in high-speed mobile applications, such as handling and transportation equipment. For this purpose, specialized equipment, including a research gantry crane, has been prepared to simulate the real operation of control and power cables on a 1:1 scale. The laboratory gantry crane is complemented by a device for testing bending resistance at ultra-low temperatures, reaching as low as −50°C.
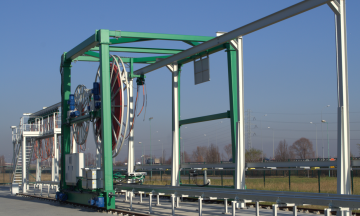
TFPowerPack is an energy storage solution that enables full energy independence. TFKable Group's solution is a key element in reducing energy costs and effectively protecting customers from power outages. TFPowerPack facilitates the implementation of solutions based on renewable energy sources, including limiting short-term power fluctuations from RES and balancing their operational profile, thus contributing to efficient CO₂ emissions reduction.
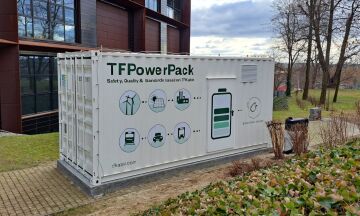
TELE-FONIKA Kable celebrated a significant milestone – the thirtieth anniversary of its founding. Over these 30 years, since beginning operations in 1992 in Myślenice, the company has consistently built a modern TFK.Group, focusing on experience, specialized knowledge, a skilled workforce, and innovation. These three decades of operations also include fruitful collaboration with partners from universities, research institutes, and international cable manufacturers' associations, which supports the development of the company and the entire industry.
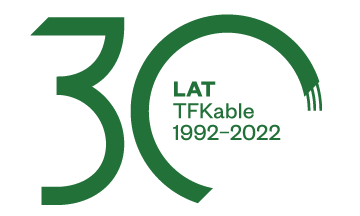
The laboratory is equipped with 5 Faraday chambers for routine and type tests of cables and cable systems. It features high voltage generators up to 1000 kV and surge generators up to 2400 kV. TFKable has two dedicated test fields for qualification tests, equipped with 500 kV and 750 kV test systems and 5000 A heating transformer sets. These state-of-the-art laboratories enable the performance of routine tests and full qualification tests for cables up to 500 kV. The laboratory also conducts research on prototypes of HVDC cables and EHVAC alternating current cables with optimized construction and technological guidelines for their production.
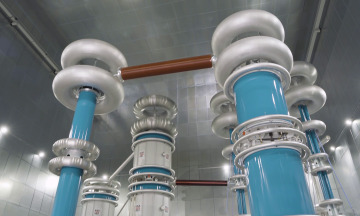
On November 11, 1920, the foundation stone laying ceremony started the history of the Bydgoszcz Plant "Kabel Bydgoszcz", currently - Zakład Bydgoszcz (Bydgoszcz Plant), TFKable Group. Nowadays, after 100 years of technology development, Zakład Bydgoszcz is the largest production center for medium, high and extra-high voltage cables in Europe (up to 500kV). Thanks to investments made over the years, Zakład Bydgoszcz delivered power cables to numerous global projects. In its rich history, the plant provided power cables for such projects as London Heathrow Airport, Channel Tunnel, Wembley Stadium, mines in Peru and Chile and the National Stadium in Warsaw.
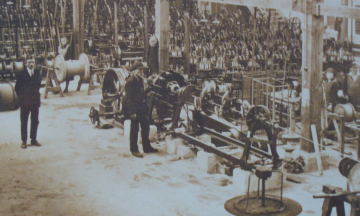
TFKable together with the partners associated in the Europacable conducted the campaign "Fire safety is our responsibility. Yours too”, related to the Construction Products Regulation (CPR). The initiative aimed to inform on a large scale about new regulations concerning cables intended for permanent installation in buildings and currently subject to the requirements of the CPR regulation. The campaign provided easy access to useful information that was intended to help installers, manufacturers, and wholesalers meet the new requirements.
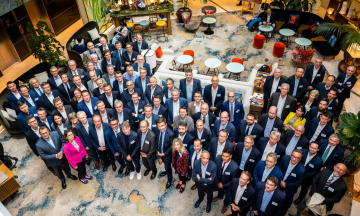
TFK.Group has implemented the TH!NK SAFETY and TH!NK QUALITY programs to raise employee awareness of safety and quality. TH!NK SAFETY enhances communication between management and operators, eliminating potential hazards, while TH!NK QUALITY focuses on minimizing costs related to quality loss through continuous process improvement. In 2018, TFKable employees submitted 561 ideas under the KAIZEN HSE initiative, while JDR received 186 improvement proposals, confirming the effectiveness of these programs.
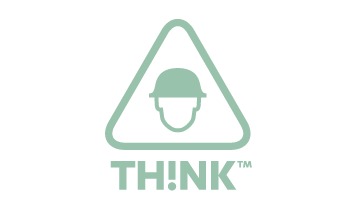
As a result of JDR’s acquisition, TF Kable has expanded its assets with two UK production facilitates, which specialize in producing subsea umbilicals and power cables, including not only energy cables but also cables used for data transmission, and monitoring and remote control of offshore facilities. Additionally, sales portfolio has been extended by technologically advanced subsea systems, maintenance and installation services, located in JDR’s centers in the US, Brazil and Singapore, ensuring constant support for our business partners.
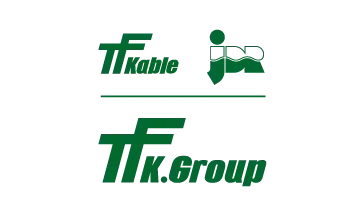
Panel: "Energy Management and Sustainability in the Cable Industry" The presentation addressed key challenges related to EU regulations and effective energy management. It highlighted the implementation of eco-friendly production technologies, resource-efficient strategies, and solutions to reduce pollutant emissions. Innovative automated production lines and advanced products, such as Flameblocker and Flamex-950, were also introduced, ensuring cable system reliability in demanding operating conditions.
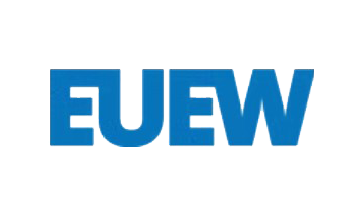
Actions, concerning the implementation of changes in relations to fire safety for cables and wires harmonized in European Standard EN 50575:2014, have been started. The implementation date for this standard was determined as of July 1, 2017.
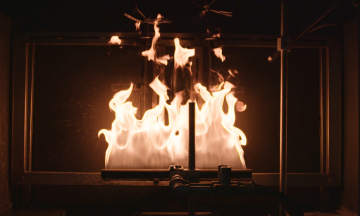
TELE-FONIKA Kable S.A. became an active member of Europacable, the association of the largest European producers of conduits and cables. Since September 2015, Mrs. Monika Cupiał-Zgryzek has been Vice-President of Europacable.
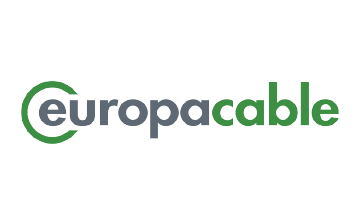
The SAP APO system was implemented for advanced production planning and scheduling for the cable industry.
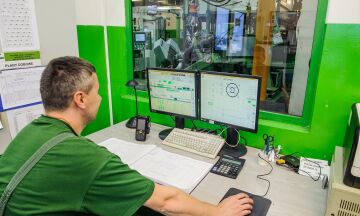
Warehouse consolidation – warehouses were centralized finished products at factories, warehouses in the Czech Republic were closed, Germany and Sweden as well elevated warehouses were created in Great Britain
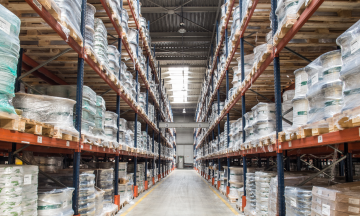
From January 2012 to February 2013, the group carried out the production specialisation project. The specialisation optimised placement of machines between and inside the plants. The aim was to create production slots limiting internal transport by shortening the production cycles and reducing the amount of stock.
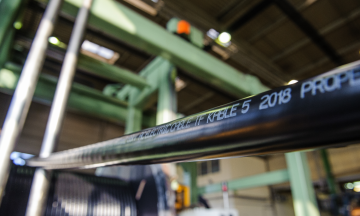
To power the National Stadium in Warsaw as one of the arenas of Euro 2012, special high voltage 110 kV cables with fibre modules were used. The cable line included a section of approximately 510 m, in which the cables were arranged under the Vistula River in a protective pipe, installed using a modern HDD (horizontal directional drilling) method.
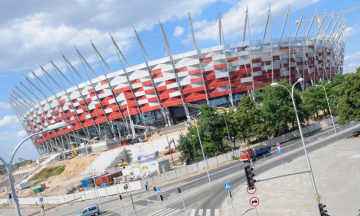
TF Kable, as the first producer in Poland and one of the few in Europe, started the production of aluminium winding conduits Al 200 in the plant in Szczecin. The conduits were used for the production of transformers. Initially, it was possible to produce conduits of 2-3.55 mm diameter; now, the diameters are 0.3-4 mm.
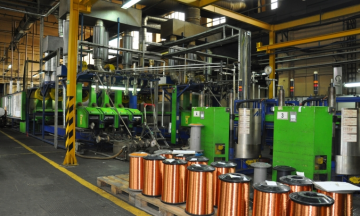
TF Kable fulfilled the first order for the production of hybrid high voltage cables of 64/110 kV. The cables included a fibre optic module to measure its temperature. Ordered cables were delivered to Chile.
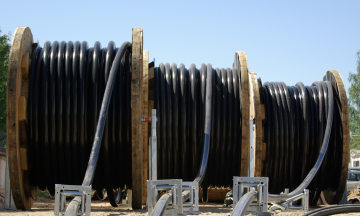
CNTK (Scientific and Technical Railway Centre) was granted the project for a high-speed, 250 km/h railway network, the construction of which involved the production of profile cables made of CuAg alloy, with the supporting lines and hanging lines produced in the plant in Kraków-Bieżanów. The team, including specialists from TF Kable, was awarded the project by the Prime Minister.
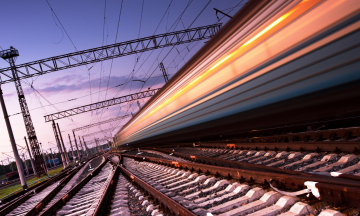
TELE-FONIKA Kable has launched the production of halogen-free FLAME-X Enhanced, Single, and POWER cables. It is the first company from Central and Eastern Europe to obtain certification from the UK certification body LPCB.
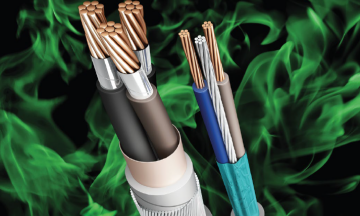
In accordance with the directives of the European Union, the Cable Waste Recycling Plant was launched in Bukowno. The plant is designed to recycle approximately 10,000 tonnes of cable waste per year. By using the latest environmentally friendly technologies, fractions of each material with a purity of over 99.5% are recovered.
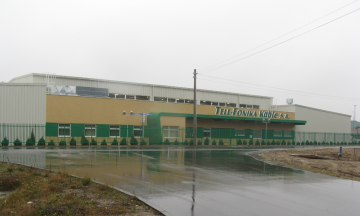
As a result of the acquisition, TF Kable now includes Fabrika Kablova Zajecar d.o.o. located in Serbia. The plant specialises in the production of low and medium voltage cables, telecommunication cables and wires.
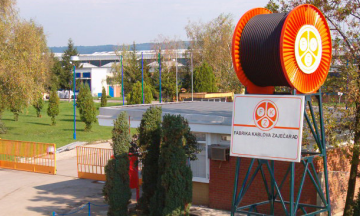
TF Kable fulfils the first order for extra high voltage cables of 127/230 kV. The cable was produced in the Bydgoszcz plant at the order of a customer from South America.
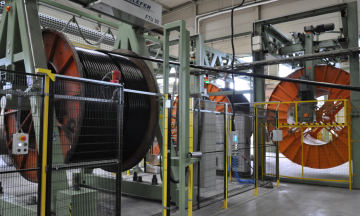
The production of mining cables of SHD and GGC types, in rubber and polyurethane coatings began at the plant in Kraków. Significant investment allowed for the installation of 15 CV lines, making the plant the largest centre for rubber cable production in Europe.
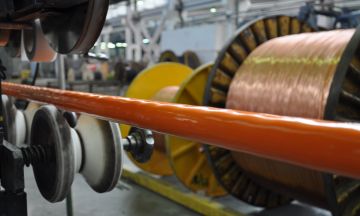
TF Kable was the first company in Poland to obtain <HAR> certificates for conduits in PVC insulation and in rubber insulation. They allow the company to mark its products with the harmonised European mark certifying that the marked conduits meet the requirements of the relevant European Standards (EN) or the harmonised documents (HD).
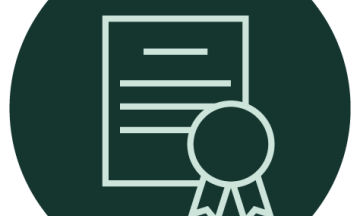
Four new production lines were developed in Bydgoszcz to produce medium and high voltage cables in XLPE insulation. The plant in Bydgoszcz became the largest producer of medium and high voltage cables in one location in Europe. In total, plant operates eight XLPE lines.
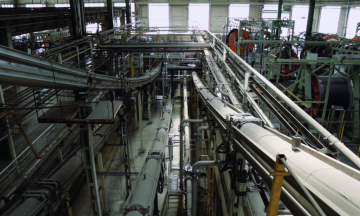
Within the structure of Zakłady Kablowe TELE-FONIKA S.A., a modern robotic plant was launched in Kraków-Bieżanów , specialising in the production of flexible multi-wire cores, aluminium mass cores produced on four lines by Holton Conform, overhead conduits made of aluminium alloy, traction conduits for high-speed “trolley” type rail and conduits in PVC for common applications.
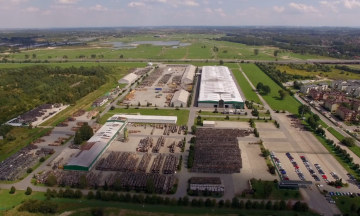
TELE-FONIKA KFK S.A. purchased the majority stake of ELEKTRIM Kable S.A. In 2003, after purchasing all shares of ELEKTRIM Kable S.A., a new entity, TELE-FONIKA Kable S.A., was established. As a result of the acquisition, TELE-FONIKA Group included: Bydgoska Fabryka Kabli (BFK), founded in 1920, specialising in the production of low, medium, high and extra high voltage cables and Fabryka Kabli Załom (FKZ), established in 1954, specialising in the production of enamelled winding conduits.
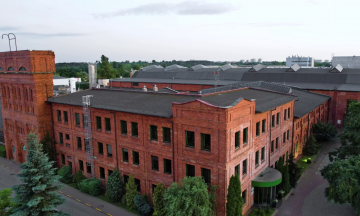
On 22 January 1999, TELE-FONIKA s.c. acquired the majority of shares in Krakowska Fabryka Kabli SA (KFK), with 100% of the company purchased by the end of 2001. The factory was established in 1928, and was the largest Polish producer of power cables and conduits. In 1992, it obtained the ISO certificate granted by BASEC, England. Rubber cables and conduits are the plant’s top products.
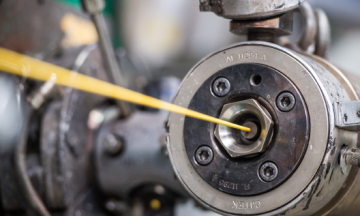
The production of modern fibre optic cables began in the plant in Myślenice after the purchase of technical equipment from Nokia Maillefer. The pace of installation and commissioning of the production line eclipsed any previously known system for producing optical fibres. At this point, the plant was ready to produce fibre optic cables with up to 860 fibres per cable
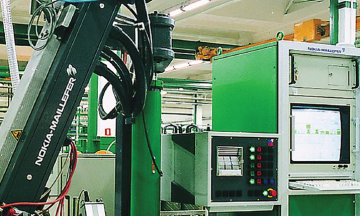
The production of modern telecommunication copper cables began in the plant in Myślenice. These four-pair computer UTP and FTP cables of cat. 5 enabled the transfer of data in a band up to 100 MHz and flow of 1 Gbit/s. The market demand was so high that the production capacity in this range doubled within a year.
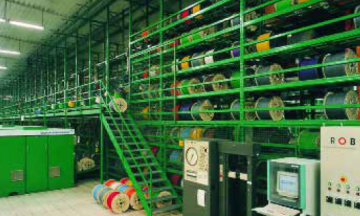
A notarial deed was signed to establish Zakłady Kablowe TELE-FONIKA s.c. on 7 April 1992 in Myślenice. Soon after, a modern plant began producing copper telecommunication, computer and fibre optic cables, within a short time becoming the leading cable producer in the Polish market.
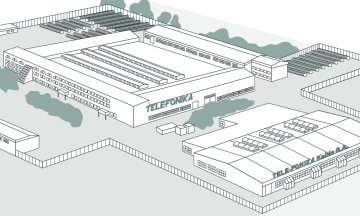